- Home
- Products
- Brushless Motor
- Brushless Motor(DC input)
- 50W Brushless Motor Driver
- Output power: 50W.
- Standard reduction ratio: 5~100 ratio.
- Power input voltage: DC24V
- Speed control range: 100~3000rpm/min.
- Protection functions: overload, overcurrent, overspeed, motor rotation, detector abnormality and other protections.
Specifications
Motor model | Round shaft type | 8BH050A-K25 | |||||||
---|---|---|---|---|---|---|---|---|---|
Pinion type | 8BH050GB-K25 | ||||||||
Driver model | BHD050-K | ||||||||
Rated output | (W) | 50 | |||||||
Power input | Rated voltage | (V) | DC24 | ||||||
Voltage tolerance | -15% ~ +15% | ||||||||
Rated input current A | (A) | 2.9 | |||||||
Maximum input current A | (A) | 5.4 | |||||||
Rated RPM | (r/min) | 2500 | |||||||
Speed control range | (r/min) | 100~3000 | |||||||
Speed change rate | - 0.5% ~ +0.5% | ||||||||
Rated torque | (N-m) | 0.19 | |||||||
Maximum torque | (N-m) | 0.29 | |||||||
Rate Time | Continuous | ||||||||
Degree of Protection | Motor: IP40 Driver: IP00 | ||||||||
Insulation class | Class B | ||||||||
Shaft material | Motor shaft, reducer output shaft: steel | ||||||||
Driver detector | Hall element | ||||||||
Insulation current protection | Motor: Coil to case DC500V 100MΩ or more Driver: Power terminal to driver heat sink DC500V 100MΩ or more |
||||||||
Insulation pressure resistance | Motor: coil to housing AC1500V/1 minute Driver: Power terminal to driver shell AC500V/1 minute |
||||||||
Usage environment | Temperature: 0 ~ +40℃ (no freezing) Humidity: below 85% (no condensation) Altitude: below 1000m above sea level Environment: No corrosive gas or dust. Do not use in explosive, radioactive places, magnetic fields, vacuum and other special environments. |
||||||||
Storage environment | Temperature: -20 ~ +70℃ (no freezing) Humidity: below 85% (no condensation) Altitude: below 3000m above sea level Environment: Avoid direct sunlight, less salt and well-ventilated place. |
Product model list
Motor model | Type | Frame number | Output power | Motor shaft type | Driver model | Power supply voltage | Corresponding gearbox | Reduction ratio |
---|---|---|---|---|---|---|---|---|
8BH050A-K25 | Brushless motor | 80mm | 50W | Round shaft | BHD050-K | DC24V | - | - |
8BH050GB-K25 | Brushless motor | 80mm | 50W | Helical gear shaft | 8GB | 5,10,15,20,30,50,100 |
Motor torque characteristics
Reducer specifications
Reducer | Deceleration ratio | 5 | 10 | 15 | 20 | 30 | 50 | 100 | ||
---|---|---|---|---|---|---|---|---|---|---|
Motor shaft speed | ||||||||||
Output shaft speed | (r/min) | 2500r/min | 500 | 250 | 167 | 125 | 83 | 50 | 25 | |
Allowable torque | (N.m) | 50W | 100~2500r/min | 0.83 | 1.65 | 2.52 | 3.30 | 4.75 | 7.95 | 16.00 |
3000r/min | 0.70 | 1.36 | 2.04 | 2.81 | 3.98 | 6.60 | 13.29 | |||
Allowable hoisting load | (N) | 50W | Distance from the front of the output shaft 10mm | 200 | 300 | 450 | ||||
50W | Distance from the front of the output shaft 20mm | 250 | 350 | 550 | ||||||
Allowable thrust load | (N) | 50W | 100 | |||||||
Operation direction | In the same direction as the motor | In the opposite direction of the motor |
External View
■ 50W Motor with Gear Box Set
Unit:mm
Ratio | L |
---|---|
5~20 | 85mm |
30~100 | 90mm |
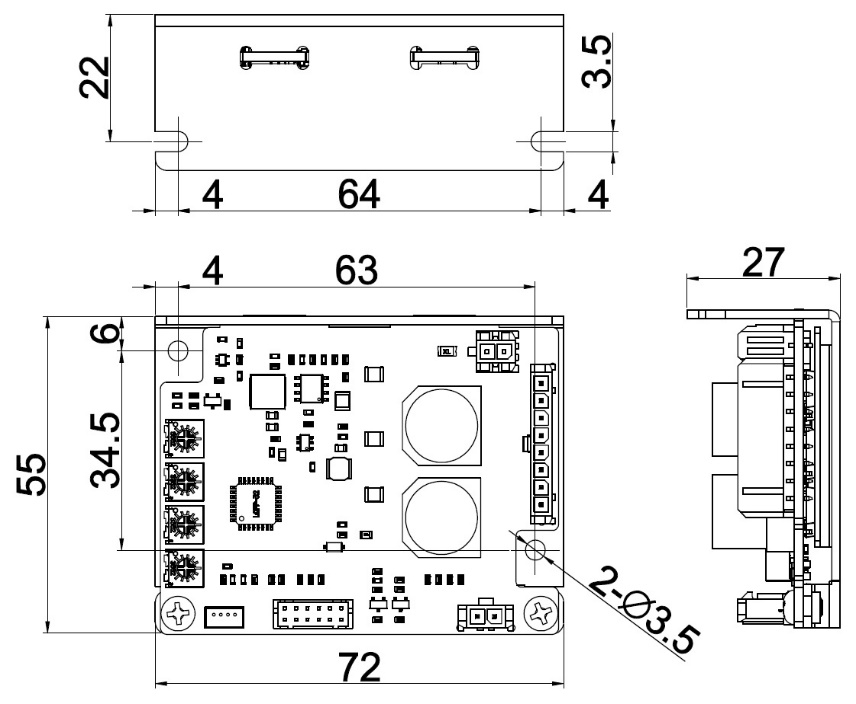
Operation Instructions
■ Driver Functions
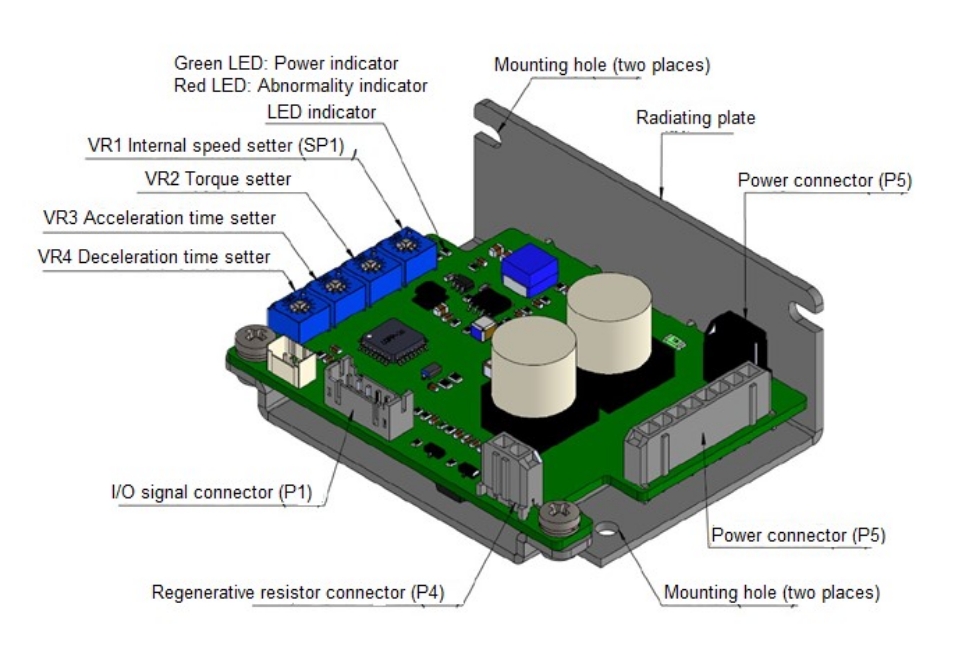
■ Functions
Functions | Content | ||
---|---|---|---|
Speed setting method | Via SP1 internal speed setter (VR1) | ||
Via SP2 external speed setter | |||
External DC voltage via SP2: DC 0~5V 1mA or more | |||
Torque range | Adjust and set the torque range through the torque setter (VR2). | ||
Acceleration time, deceleration time* | Set within the range of 0.1~12 seconds | ||
Settings can be made using the acceleration time setter (VR3) and deceleration time setter (VR4). | |||
*The actual acceleration time and deceleration time are affected by the customer's usage conditions, load inertia and load torque, etc. | |||
Input signal | START/STOP input, RUN/BRAKE input, switching of running direction, selection of internal or external speed setting, setting of torque range, input of ALARM-RESET. | ||
Regenerative resistor | Connectable pick-up resistor connector (P4) | ||
Output signal | SPEED output, ALARM output | ||
Protection function | Overload, motor detector abnormality, overvoltage, undervoltage, overspeed, motor stall, driver abnormality, initial start abnormality. |
Note: Please refer to the BU series operation manual for relevant details.